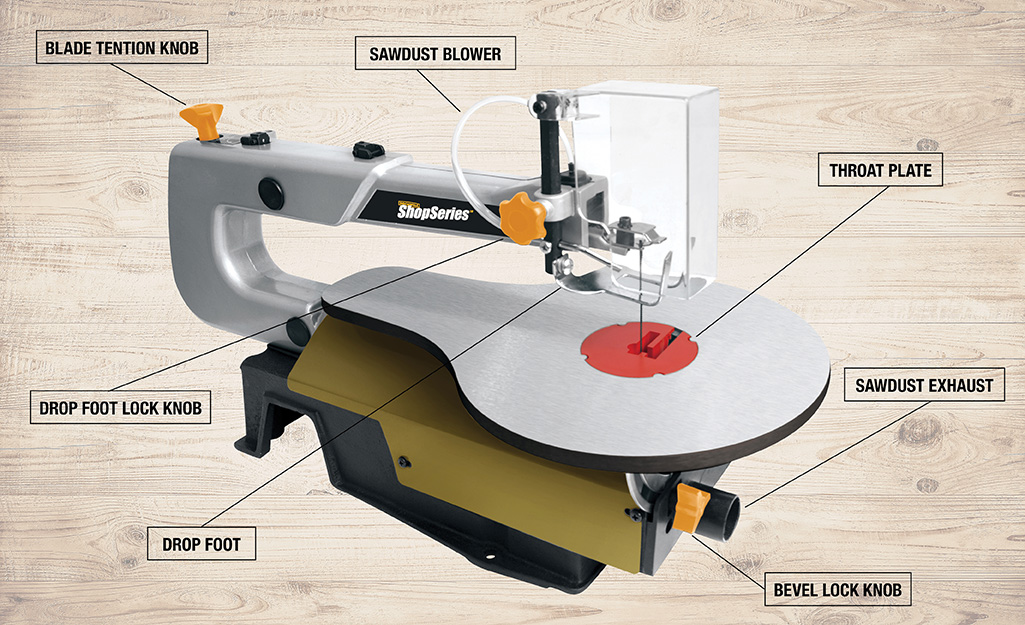
If fretwork is something you enjoy, then you might have wondered how you could create your very own. Fretwork patterns allow you to do exactly that. These unique designs are created independently by artists, and printed on high-quality materials in an ethical and responsible manner. Every purchase helps the artist and funds their work. This article will demonstrate how to create your fretwork pattern. You can start in no time.
Inlay cutting
Inlay cutting, a popular technique in guitar construction, is very common. The technique is a great way to use up small pieces of wood. You may even want to try marquetry, which is a method of adding decorative pieces to a wood game board. In either case you will need to practice until it becomes a habit. Inlay cutting with an electric guitar is simple and fast. Here are some steps to create stunning inlays.
Tracing outlines
If you're working in a boat, you will need to trace the outline for fretwork patterns. This can be done by either placing the pattern sheet directly on the board or by placing a piece of carbon between them. You can trace the pattern to create the shape of the fretboard you want. This is a better option to pasting patterns as you can trace each fretboard part without worrying about lines. You can trace the patterns by using a pencil to draw the shapes. The letters will be labelled and the pieces next to them will have the exact same appearance.
Cutting
An acorn chair can be made easily by anyone who has a few fretwork skills. It is a sturdy, elegant piece of furniture. The pattern sheets for the acorn chairs are printed at full size and double the size of their actual design sheets. The entire set includes all necessary parts such as planed boards with the right thickness, seat edges, carriage racks, steps, and carriage racks. Extra thick undercarriage is required for the axle and footboard.
Polishing
If you are making fretwork on an instrument, you'll probably want to know how to polish fretwork patterns. If your frets aren't polished at all, it can look like a blot on the surface. There are some things you can do to help the process go smoothly. First, make sure you have a flat panel for your work. Once that's achieved, you can start polishing the fretwork.
The addition of a room
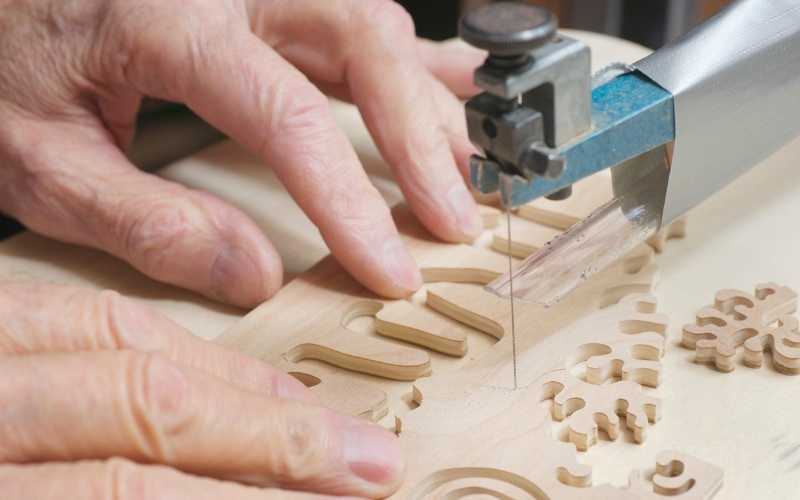
The addition of fretwork patterns can bring depth and movement into a room. These patterns can be used for stencils when you want to paint or design fabric. These patterns can also be used as stencils to design fabric or paint a wall. It is a wonderful way to add dimension to your space without adding too much. In addition, fretwork patterns can be used as focal points to create a garden-like atmosphere.
Furniture
The look of furniture with fretwork patterns can add a touch of class to any room. These patterns look especially good with pieces in solid colors. You can update classic shapes with these patterns to give them a modern look. They are also a great way to update the look of an interior that has lost its originality. Here are some examples. Below are the most popular types of fretwork.
Walls
Placing wall panels with fretwork patterns on the walls is a great idea to add personality to a space and to add subtle texture to focal point points like the ceiling. They're lightweight, water-resistant, and won't warp, bubble, or rot. They are removable and can be used as accent walls. They come with 4 sizes.
Curtains
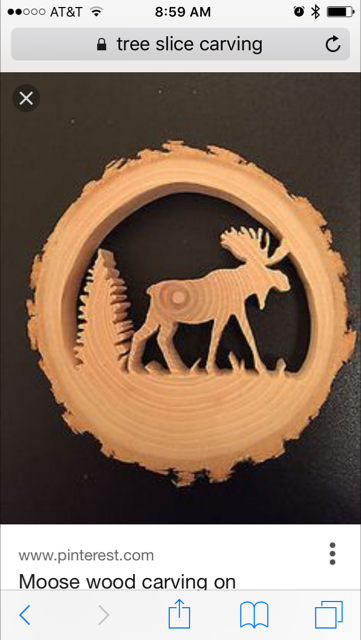
Window curtains with fretwork patterns can be a beautiful decorative addition to any home. This design is attractive and functional. Some designs include intricate fretwork that can be a conversation-starter in your home. Designer Living is one of the best places to find fretwork patterns on curtains. To get the perfect design for your home, here are some things to keep in mind before purchasing these curtains.
FAQ
How can a beginning woodworker make a living?
Many people learn how to make furniture in order to set up an online business. But if you're just getting started building furniture, there are other ways to earn money besides selling on Etsy. Local craft fairs and events are great places to sell your products. You could also offer workshops to help others learn how to make their own furniture. Consider offering your services if you have previous experience as a builder or carpenter.
How can you calculate the woodworking price?
When calculating the costs of any project, it is important to keep them as low and affordable as possible. Always ensure you are getting the best possible price for materials. Also, consider all other factors that can affect the price of your projects such as skill level, experience, time and cost. Our guide to the average household DIY task price will give you an idea of how much it costs to complete different types of woodwork projects.
What's the time taken to finish a piece furniture?
It depends on the size of the piece of furniture. A smaller project like picture frames or boxes can be completed in a single day. Larger projects such as tables and desks can take several days to complete. It takes time to properly stain and seal wood.
How often do I need to buy new supplies
You may have to replace certain tools. If you are using hand tools, you will need to sharpen them frequently. If you are using power tools, you will need to purchase replacement parts regularly. Spread your purchases over several months to avoid purchasing too many items at once.
How much should a hobbyist invest to get started?
A lot of capital is required to purchase the necessary supplies and tools if you want to start your own woodworking shop. You can start by purchasing a small table saw and drill press as well as a circular saw, circular saw, jigsaw and sanding machines. These items are affordable so you won’t break the bank.
Statistics
- Woodworkers on the lower end of that spectrum, the bottom 10% to be exact, make roughly $24,000 a year, while the top 10% makes $108,000. (zippia.com)
- The U.S. Bureau of Labor Statistics (BLS) estimates that the number of jobs for woodworkers will decline by 4% between 2019 and 2029. (indeed.com)
- If your lumber isn't as dry as you would like when you purchase it (over 22% in Glen Huey's opinion…probably over 10-15% in my opinion), then it's a good idea to let it acclimate to your workshop for a couple of weeks. (woodandshop.com)
- The best-paid 10 percent make $76,000, while the lowest-paid 10 percent make $34,000. (zippia.com)
External Links
How To
Here are some tips on how to drive nails in wood
First, choose the right size and type of tool to drive a nail through wood. The most common types of hammers are claw hammers, sledgehammers, mallets, ball peen hammers, and hatchets. Each type of tool has its advantages and drawbacks. A clawhammer works best when hitting something hard like nails. However, it can sometimes be difficult to see exactly where the strike is going. The sledgehammer works well for large areas, but is too heavy for smaller tasks.
After choosing the right hammer, place your hand flat against the side of the head so that the handle rests comfortably in your palm. Grip the handle firmly, but don't squeeze it so tightly that you hurt yourself. Your wrist should be relaxed while you hold the hammer straight upwards. Swing the hammer back towards the ground, with your aim at the middle of the nail. You should feel the impact of your hammer hitting the nail. Practice swinging your hammer on a block of wooden until you feel comfortable.
Hold the hammer near your body until you're ready for the nail to be driven. Position the nail, so it's perpendicular to the surface of the wood. Keep your eyes on the tip. Swing the hammer forward, and then move the hammerhead. Continue this motion several times, slowly increasing the speed of each swing. Once you have mastered this technique, increase the power of your swings. To make it more powerful, hold the hammer up high to your shoulder and then bring it down. You will be able to use more energy and put your best foot forward.
Once you've nailed the first hole, remove the hammer from the nail. To remove the remainder of the nails, you can use a screwdriver/pry bar. To prevent splitting the wood, ensure you keep the nail heads flush against the board's surface.